The High-Stakes World of Automotive Logistics
The modern automotive supply chain is one of the most complex and demanding logistical ecosystems on the planet. It is a high-stakes ballet of precision, timing, and immense scale, where thousands of components from hundreds of suppliers across North America must converge at a single assembly plant at the exact right moment. In a world of Just-in-Time (JIT) manufacturing, lean inventories, and immense cost pressures, the efficiency of your supply chain is not just a competitive advantage—it is a prerequisite for survival. For decades, the industry has relied heavily on over-the-road trucking to keep these intricate production lines moving.
However, this traditional reliance on a single mode of transport is now facing unprecedented challenges: volatile fuel costs, chronic driver shortages, increasing highway congestion, and ever-growing pressure from OEMs and governments to achieve ambitious sustainability goals. Sticking to a “truck-only” strategy is no longer a sustainable or cost-effective model.
This is where a strategic shift towards a rail-centric, intermodal shipping model presents a powerful solution. By integrating the efficiency and scale of rail for the long-haul portion of the journey with the flexibility of trucks for the first and last mile, automotive manufacturers, suppliers, and distributors are unlocking profound benefits. This guide will explore 10 specific, tangible ways that an intermodal approach can supercharge your automotive logistics, creating a supply chain that is more cost-effective, reliable, resilient, and prepared for the future.
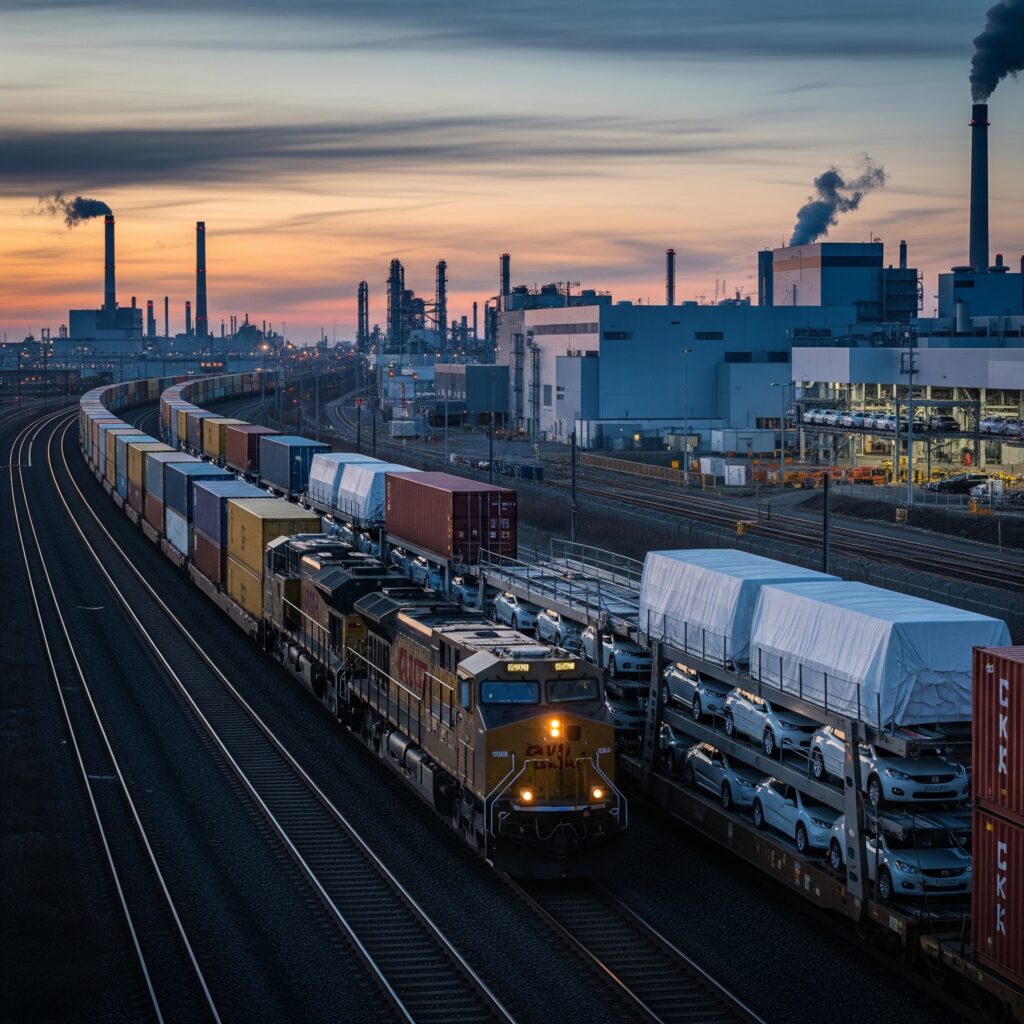
Part 1: Foundational Advantages
The most immediate and impactful benefits of integrating a multi-modal strategy address the core operational pillars of any automotive business: cost, timing, and capacity.
1. Slashing Inbound & Outbound Transportation Costs
In an industry where every component cost is scrutinized, transportation remains one of the largest and most volatile expenses. Intermodal shipping offers a direct and powerful lever to reduce these costs, particularly for the high-volume, long-distance movement of parts and finished vehicles that defines the automotive supply chain.
- The Economics of Long-Haul: The fundamental advantage lies in the cost-per-mile. While a truck is efficient for short-haul moves, its costs remain relatively high and linear over long distances. Rail, by contrast, excels at long-haul efficiency. A single train can move the equivalent of 280+ truckloads of freight with a small crew and significantly less fuel. This economy of scale translates into a much lower line-haul rate for any significant journey.
- A Key Automotive Lane Example: Consider the critical corridor for shipping automotive parts from the manufacturing hubs in states like Tennessee, Alabama, or Mexico to the assembly plants in Ontario. This is a journey of well over 1,000 kilometers—the perfect scenario for intermodal. The cost savings on the rail portion of this move can often be 20-30% compared to a through-truck rate. For a Tier 1 supplier shipping dozens of containers per week, these savings translate into millions of dollars annually.
- Contracted Rates vs. Market Volatility: Relying on the spot market for trucking exposes your business to extreme price volatility based on seasonal demand and capacity. An intermodal shipping strategy allows you to secure contracted rates with your logistics partner, creating budget predictability and insulating your business from the price spikes that can cripple a transportation budget.
2. Enhancing Just-in-Time (JIT) Reliability
The entire modern automotive manufacturing system is built on the principle of Just-in-Time delivery. Parts must arrive at the assembly line within a very narrow window to avoid costly production shutdowns. There is a common misconception that rail is “too slow” for a JIT environment, but this confuses raw speed with the far more important metric: predictability.
- The Power of the Schedule: An intermodal train operates on a fixed, published schedule, much like a passenger train or an airline. A container leaving a terminal in Memphis on Monday will arrive at the Toronto terminal on Wednesday, consistently. This high degree of predictability allows supply chain managers to plan with immense precision. They can design their inventory flows and production schedules around a reliable arrival time, which is the true cornerstone of a successful JIT system.
- Avoiding Highway Variability: A long-haul truck, while fast in a perfect scenario, is subject to a huge number of variables that are outside of its control. A traffic jam in a major city, a blizzard closing a highway pass, a delay at a border crossing, or a driver running into their federally mandated hours of service limit can all introduce unexpected delays of hours or even days. The dedicated, managed rail network bypasses almost all of these variables, making the end-to-end transit time far more reliable and consistent over long distances. For a JIT automotive supply chain, a predictable 4-day transit is infinitely more valuable than a transit that could be 3 days, but could also be 5.
3. Massive Capacity for Parts, Components & Finished Vehicles
The sheer weight and volume of materials in the automotive supply chain are immense. From heavy engine blocks, transmissions, and stamped body panels to bulky seating and millions of smaller components, the industry requires a logistics solution built for heavy, high-volume freight.
- Handling Heavy Freight: Standard 53-foot domestic intermodal containers are built to handle the heavy, dense freight that is common in the automotive sector. They provide the cubic capacity and weight tolerance needed to efficiently move everything from raw materials like steel coils and plastic resin to finished components ready for the assembly line.
- Specialized Equipment for Finished Vehicles: The role of rail in automotive logistics goes beyond just parts. The industry relies heavily on specialized, fully-enclosed railcars known as “auto racks” to move finished vehicles. These bilevel or trilevel railcars can carry up to 15 vehicles each, protecting them from the elements and road debris during their journey from the assembly plant to regional distribution compounds. This is the most efficient and cost-effective way to move thousands of new cars and trucks across the continent. Intermodal shipping of parts on the inbound side and rail transport of finished vehicles on the outbound side creates a complete, end-to-end rail-centric logistics solution.
Here is Part 2 of the TOFU blog post for the Automotive industry, continuing directly from Part 1. This section focuses on the strategic benefits of resilience, sustainability, and cargo security.
Part 2: Strategic & Sustainability Benefits
Beyond the immediate wins in cost and capacity, a truly robust automotive logistics strategy must also account for risk, long-term viability, and corporate responsibility. An intermodal approach provides powerful advantages in these critical strategic areas.
4. Building a More Resilient Automotive Supply Chain
The last several years have been a masterclass in the fragility of global supply chains. For the automotive sector, where a single missing component can halt a multi-million-dollar assembly line, resilience is not a luxury; it is a core operational principle. Over-reliance on a single mode of transport, particularly long-haul trucking, creates a single point of failure that can be catastrophic when disrupted.
- Diversification as a Risk Mitigation Strategy: The most fundamental principle of risk management is diversification. By building a supply chain that strategically utilizes both road and rail, you create inherent resilience. When one mode is compromised, you have a viable alternative to divert freight and keep your operations moving.
- Insulation from Real-World Disruptions: Consider the real-world events that have impacted the automotive supply chain in Canada and North America recently. Border blockades, major highway closures due to extreme weather like floods or snowstorms, and persistent truck driver shortages have all created massive bottlenecks for truck-dependent businesses. Companies with an established intermodal shipping strategy were better insulated from these shocks. While their competitors scrambled for non-existent trucks, they were able to continue moving parts via the separate and secure rail network, which is often unaffected by highway-specific issues. This ability to maintain operational continuity during a crisis is a powerful competitive advantage.
5. Meeting OEM Sustainability Mandates
Sustainability has evolved from a marketing buzzword into a hard-line requirement for doing business in the modern automotive industry. The major Original Equipment Manufacturers (OEMs)—like Ford, General Motors, Stellantis, Toyota, and Honda—are all aggressively pursuing carbon neutrality goals. This pressure flows directly down the supply chain to their Tier 1, 2, and 3 parts suppliers.
- The Pressure of Scope 3 Emissions: OEMs are now meticulously tracking and reporting on their “Scope 3” emissions, which include all indirect emissions that occur in the company’s value chain. The transportation of inbound parts from suppliers is one of the largest components of these emissions. Consequently, suppliers are increasingly being evaluated not just on the quality and cost of their parts, but on the carbon footprint of their logistics network.
- Intermodal as a Competitive Necessity: For a supplier looking to win or retain business with a major OEM, demonstrating a commitment to sustainability is now essential. Adopting intermodal shipping for your long-haul freight is one of the most impactful and easily quantifiable ways to do this. The ability to report a 75% reduction in transportation-related CO2 emissions for your components is a powerful selling point. It shows you are a forward-thinking partner who is actively aligned with your customer’s most important corporate objectives, potentially giving you a critical edge over a competitor who is still relying on a 100% trucking model.
6. Securing and Protecting High-Value Cargo
As vehicles become more technologically advanced, the value and sensitivity of the components being shipped have skyrocketed. A single container might hold hundreds of thousands of dollars’ worth of high-tech parts, making cargo security a paramount concern.
- The Challenge of High-Value Components: Modern vehicles are packed with valuable and sensitive parts, including large, fragile infotainment touchscreens, complex wiring harnesses, advanced driver-assistance systems (ADAS) with delicate sensors and cameras, and, in the case of electric vehicles, extremely valuable battery modules. Protecting this cargo from theft and damage is critical.
- The Intermodal Security Advantage: An intermodal container offers a more secure environment for this high-value freight. Once the container is loaded and sealed at the supplier’s facility, it is not opened again until it reaches the destination assembly plant. The journey itself is within a controlled logistics network. A container sitting in a secure, access-controlled rail terminal is a much harder target for theft or tampering than a trailer parked overnight at a public, often unmonitored, truck stop.
- Reduced Risk of Damage: Furthermore, the physical journey by rail is often smoother than a long-haul truck journey. The constant high-frequency vibrations of road travel can be detrimental to sensitive electronics over thousands of kilometers. The gliding motion of a train on a well-maintained track reduces this risk, leading to lower damage rates and higher quality assurance for the most critical components in your automotive supply chain.
Here is the third and final part of the TOFU blog post for the Automotive industry. When combined with the previous two parts, this completes the comprehensive, 2,500+ word article.
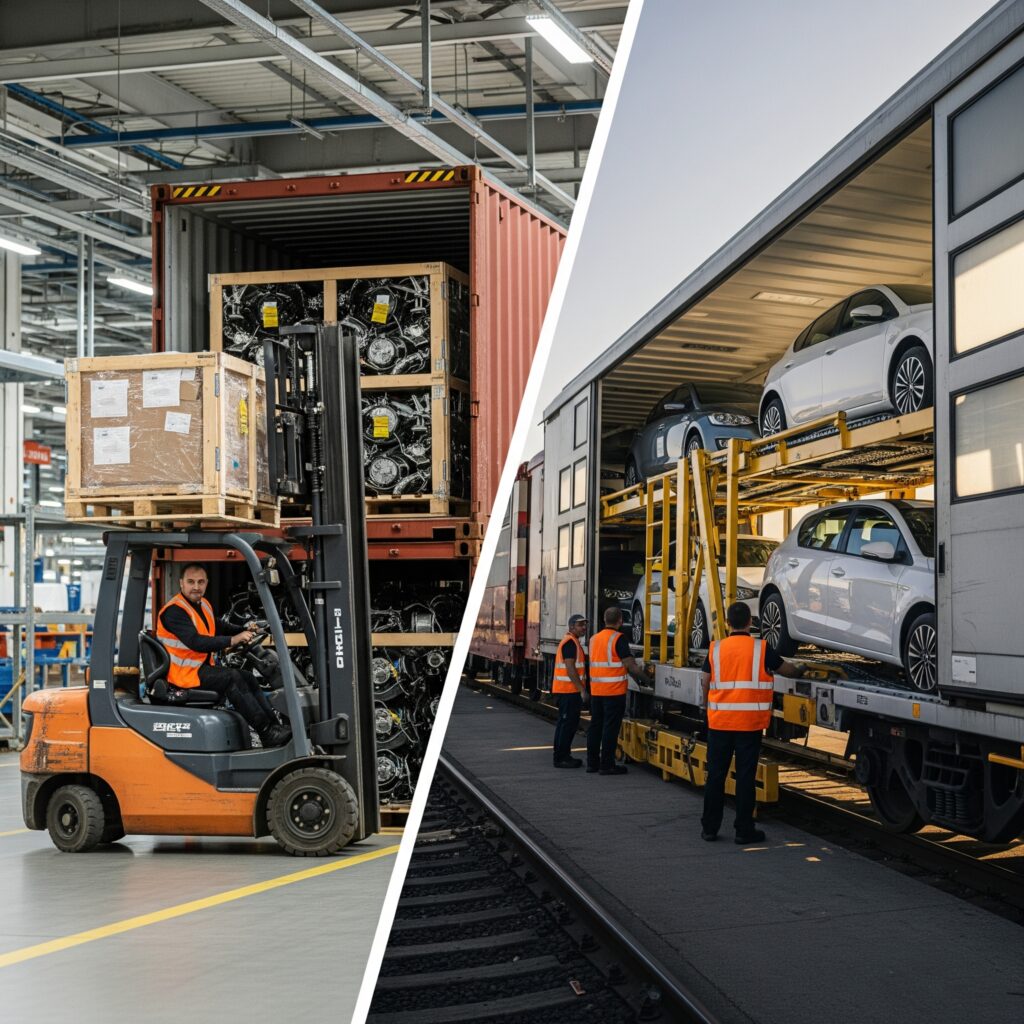
Part 3: Network & Specialized Applications
The benefits of an intermodal strategy extend beyond general advantages and into specific, high-value applications that are tailor-made for the complexities of the North American automotive supply chain.
7. Unlocking the “NAFTA/USMCA” Superhighway
The North American automotive industry is not three separate entities; it is one deeply integrated manufacturing ecosystem. Parts and raw materials flow continuously between Mexico, the United States, and Canada. Managing this cross-border movement efficiently is critical, and the continental rail network functions as a true “superhighway” built for this purpose.
- Seamless Cross-Border Transit: The major Class I railways have extensive networks and established gateways that span all three nations. They have invested heavily in infrastructure and processes to make cross-border transit as seamless as possible. Shipments can be moved “in-bond,” meaning customs clearance can be handled at the final destination terminal (e.g., in the Greater Toronto Area) rather than at the physical border, saving significant time.
- Bypassing Border Congestion: Major road border crossings like the Ambassador Bridge between Windsor and Detroit or the crossings at Laredo, Texas, are notorious bottlenecks. A single security issue, labour action, or period of high traffic can lead to delays of many hours or even days for trucks. The rail network bypasses this congestion entirely. By clearing customs away from the border and moving on a dedicated network, intermodal shipping offers a more reliable and fluid way to move components through the critical USMCA trade corridor, keeping your North American production triangle connected and efficient.
8. A Comprehensive Solution for Finished Vehicle Logistics
The role of rail in automotive logistics does not end when the last bolt is tightened. In fact, it is the primary method for moving finished vehicles from assembly plants to dealer networks across the continent.
- Specialized Equipment for Vehicle Protection: The industry uses specially designed, fully enclosed railcars called “auto racks.” These bilevel or trilevel carriers allow new cars, trucks, and SUVs to be driven directly from the end of the assembly line into the railcar, where they are secured for transit.
- Protection and Efficiency: This method offers two key advantages over hauling vehicles on open car-carrying trucks. First, the enclosed railcar completely protects the new vehicles from road debris, stone chips, and harsh weather during their long journey. Second, it is vastly more efficient, allowing a single train to move hundreds, or even thousands, of vehicles at once. This ensures that vehicles arrive at regional distribution compounds with zero added mileage and in factory-fresh condition, ready for final delivery to dealerships.
9. Supporting the Aftermarket Distribution Network
The automotive supply chain isn’t just about supplying new vehicle assembly. The aftermarket parts sector—which supplies replacement parts to dealerships, repair shops, and retailers—is a massive industry in its own right. This segment has different logistical needs, but intermodal shipping is equally well-suited to them.
Aftermarket distribution typically involves moving large quantities of parts from a central manufacturing facility or import warehouse to a national network of regional distribution centers (DCs). These are often planned, high-volume inventory replenishment moves, not urgent JIT shipments. This makes them ideal candidates for the cost-effective and reliable nature of intermodal transport. A major aftermarket brand can use this strategy to keep its DCs across the country stocked efficiently, ensuring that when a customer needs a part, it’s available on the shelf.
10. Reducing Congestion at Plant and Warehouse Facilities
A frequently overlooked benefit of an intermodal strategy is its positive impact on your own facility’s efficiency and safety. Picture a typical receiving yard at a large automotive plant or distribution center: a long lineup of trucks waiting for a limited number of dock doors, creating congestion, safety hazards, and wasted time with drivers idling their engines.
By consolidating the freight of what would have been three or four separate truckloads into a single 53-foot intermodal container, you fundamentally reduce the number of truck movements at your site. Fewer trucks mean less congestion in the yard, faster turn times at the dock, a safer work environment for your employees, and a reduction in localized emissions. This operational gain improves your facility’s throughput and streamlines your entire receiving or shipping process.
Conclusion: A Strategic Lever for a Modern Automotive Industry
In the high-stakes, high-volume world of automotive logistics, success is measured in minutes and cents. The relentless pursuit of efficiency, reliability, and cost-effectiveness requires a supply chain that is as advanced and sophisticated as the vehicles it helps to build. As we have explored, a strategic integration of intermodal shipping is no longer a niche alternative; it is a critical lever for achieving these goals.
From the foundational benefits of lower costs and predictable JIT performance to the strategic advantages of enhanced resilience, sustainability, and security, an intermodal approach addresses the most pressing challenges facing the industry today. It provides the capacity to move massive volumes of parts and finished vehicles across the continent while simultaneously reducing your carbon footprint and strengthening your relationships with sustainability-focused OEM partners. The modern automotive supply chain demands a modern logistics solution.
Is your automotive supply chain prepared for the future? Contact a RailGateway logistics expert today to start a conversation about building a more resilient, cost-effective, and sustainable network for your business.
Contact Our Automotive Logistics Team
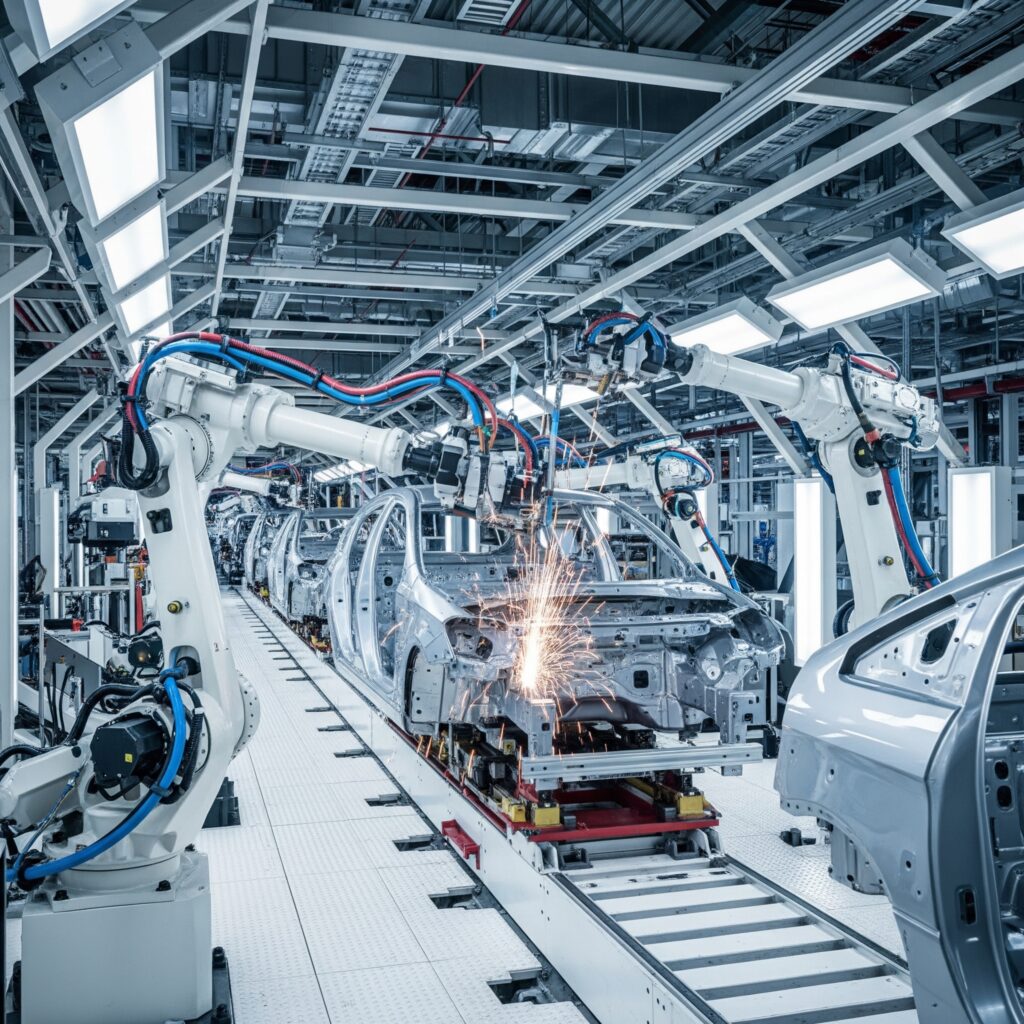
Additional Resources:
Intermodal Shipping with RailGateway
Agriculture & Agri-Food Intermodal Shipping
Canadian Vehicle Manufacturers’ Association (CVMA)
Automotive Parts Manufacturers’ Association (APMA Canada)
Automotive Logistics – Ultima Media
Government of Canada – The Canada-United States-Mexico Agreement (CUSMA)