From Potential Benefit to Practical Decision
You have moved past the initial discovery phase. You understand the core concept of intermodal shipping and recognize its potential to address some of the most persistent challenges in the modern automotive supply chain. The foundational knowledge is there. Now, you’ve arrived at a critical decision point where strategy must translate into action. The core dilemma facing every logistics and supply chain professional in the automotive sector is this: When does the familiar, flexible model of dedicated Full Truckload (FTL) shipping remain the right choice, and when do the strategic advantages of an integrated intermodal shipping network present a superior business case?
Making this decision requires moving beyond a simple overview and into a direct, head-to-head comparison of the two modes. This is not about abstract benefits; it’s about how each method performs under the intense pressure of Just-in-Time (JIT) production schedules, complex cross-border parts movements, and relentless cost-down pressure from OEMs.
This guide is built for this purpose. We will dissect and analyze seven critical factors, providing a clear, balanced comparison of intermodal versus trucking. Our goal is to equip you with the data and perspective needed to confidently determine the optimal logistics strategy for your specific automotive logistics needs.
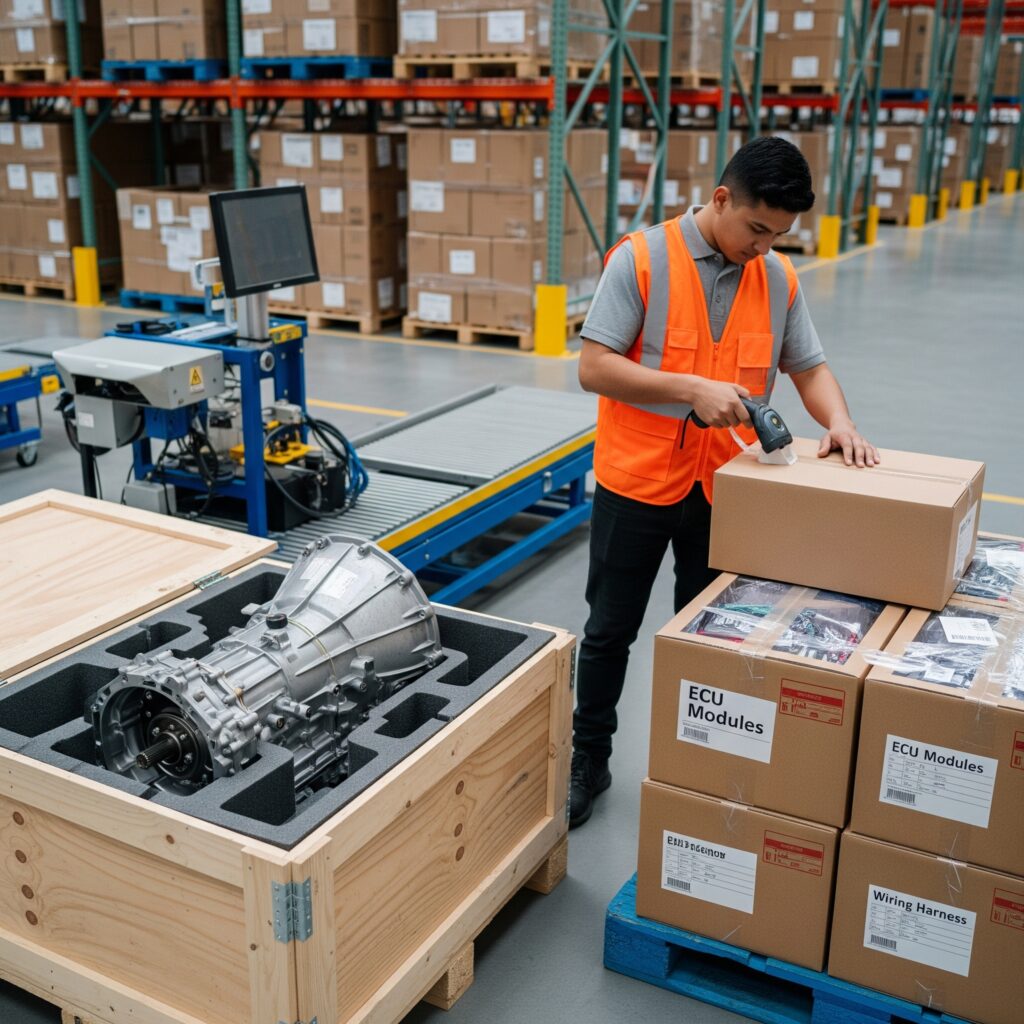
Part 1: The Core Operational Comparison
Let’s begin by comparing the two modes across the three pillars of automotive operational performance: cost, timing, and capacity.
Factor 1: The Cost Equation for High-Volume Parts
In an industry where every penny per part is scrutinized, transportation costs are a major focus. The choice between intermodal and trucking has a profound and direct impact on your landed cost. To make an informed comparison, you must look beyond the surface and analyze the total cost structure.
- The FTL Cost Model: The cost of a dedicated truck is driven primarily by a per-mile rate, a volatile fuel surcharge, and labor. For the long, high-volume lanes typical of the automotive supply chain (e.g., moving transmissions from Mexico to Michigan, or electronics from California to Ontario), these costs add up quickly and can be unpredictable.
- The Intermodal Cost Model: An intermodal move has a different structure, composed of the initial truck move to the rail terminal (drayage), the highly efficient long-haul rail journey, and the final delivery truck move. The key to the savings is the rail portion. The economies of scale are so immense that for any significant distance, the savings on the line-haul and fuel surcharge far outweigh the cost of the drayage at either end.
Let’s illustrate with a critical automotive lane: Silao, Guanajuato, Mexico to Windsor, Ontario, Canada.
Cost Component | Full Truckload (FTL) | Intermodal Shipping | Analysis |
Line-Haul & Border Crossing | ~$7,000 | ~$5,000 | The rail network is built for this cross-border “superhighway,” offering significant structural savings on the longest leg of the journey. |
Fuel Surcharge (FSC) | ~$1,400 | ~$700 | Due to rail’s superior fuel efficiency, the FSC is roughly half that of a truck, providing a crucial hedge against volatile energy prices. |
Drayage (First/Last Mile) | N/A | ~$800 | This is the added cost for intermodal, but as shown, it’s a small price to pay for the immense line-haul and fuel savings. |
Total Estimated Cost | ~$8,400 | ~$6,500 | ~22% Estimated Savings with Intermodal |
Export to Sheets
Disclaimer: These are illustrative estimates. Actual market rates vary.
For any Tier 1 or Tier 2 supplier shipping parts regularly on these long-haul North-South corridors, a 22% cost reduction is a massive competitive advantage and a significant boost to the bottom line.
Factor 2: Just-in-Time (JIT) Performance: Speed vs. Predictability
This is, without question, the most critical operational concern for automotive logistics. The fear of shutting down an assembly line because a shipment is late is what keeps supply chain managers up at night. The debate, however, should not be about raw speed, but about a far more valuable metric: predictability.
- The Illusion of FTL Speed: In a perfect, theoretical scenario with no traffic, no weather, and no delays, a team of two drivers can get a truck from A to B faster than an intermodal shipment. This makes FTL the right choice for true “hot shot” emergencies. However, the North American highway system is rarely a perfect scenario. A single accident can cause a 4-hour traffic jam. A snowstorm can close a highway for a day. A driver can run out of service hours. This introduces a high degree of variability. A shipment that is scheduled for 4 days can easily become 5 or 6 days old with little warning.
- The Power of Intermodal Predictability: Intermodal shipping operates on a different paradigm. Trains run on a fixed, published schedule. While the door-to-door transit time might be scheduled for 5 or 6 days on a long lane, that schedule is remarkably consistent. The train is not affected by highway traffic. The network is designed to operate 24/7 through nearly all weather conditions. This operational consistency allows a plant manager or materials planner to design their production schedule with a high degree of confidence. For a JIT system, knowing a shipment will reliably arrive in 5 days is infinitely better for planning and inventory management than knowing a shipment might arrive in 4 days, but could also arrive in 6. Predictability is the true engine of Just-in-Time manufacturing.
Factor 3: Capacity & Scalability for Production Ramps
The automotive industry is characterized by cycles, including new model launches, production ramp-ups, or seasonal demand shifts that require a sudden and significant increase in the volume of inbound parts. The ability to scale your logistics capacity to meet this demand is crucial.
- The FTL Capacity Challenge: When you need to suddenly increase your shipment volume from 10 trucks a week to 30, you are thrown into the volatile spot market. You must compete with every other shipper for a limited pool of available trucks and drivers. This inevitably leads to skyrocketing prices and, in many cases, the inability to secure the capacity you need at any price, putting your production ramp-up at risk.
- The Intermodal Capacity Solution: The rail network is inherently designed for high-volume movements. Scaling capacity with intermodal shipping is a far more structured and less frantic process. It’s not about finding 20 more individual trucks; it’s about reserving 20 more slots on trains that are already scheduled to run. By working with a logistics partner, you can provide a forecast for your production ramp-up and secure large blocks of capacity in advance, often at a contracted rate that protects you from spot market surges. This transforms a potentially chaotic logistics scramble into a smooth, managed, and cost-controlled process, ensuring your supply chain can seamlessly support your company’s growth.
Part 2: Risk, Security, and Sustainability
Beyond the core operational metrics, a truly strategic logistics decision must also account for risk mitigation, efficiency at critical chokepoints, and alignment with the long-term goals of the entire industry.
Factor 4: Cargo Security for High-Value Components
As vehicles evolve into “computers on wheels,” the value of the components being transported has increased exponentially. A single container may hold millions of dollars in sensitive electronics, making cargo security a top-tier concern for risk management in any automotive supply chain.
- The FTL Security Model & Its Vulnerabilities: When a truck undertakes a long-haul, multi-day journey, drivers are required by law to take mandatory rest breaks. These often occur at public truck stops or unsecured rest areas along the highway. These locations are known vulnerabilities, targeted by sophisticated cargo theft rings that look for high-value loads. A trailer full of infotainment systems, ADAS sensors, or EV battery components sitting unattended overnight is a significant liability. Furthermore, the constant vibration and potential for shocks on a highway journey can pose a risk to delicate electronic components, potentially leading to a higher rate of quality-control failures upon arrival.
- The Intermodal Security Model: A Layered Approach.Intermodal shipping offers a fundamentally more secure environment.
- The Sealed Container: Your parts are sealed in an anonymous steel container at your facility. This container is not opened until it reaches the destination.
- The Secure Network: The container spends the vast majority of its journey within a highly controlled and monitored network. Rail terminals are private, fenced, lit, patrolled by railway police, and monitored by extensive camera systems. This “secure yard” environment drastically reduces the opportunity for theft or tampering compared to a public rest stop.
- A Smoother Ride: The physical ride on a train is significantly smoother, with fewer high-frequency vibrations than a highway journey. For sensitive electronics, this can mean a lower rate of transit-related damage, ensuring the components arrive in perfect operational condition.
For high-value automotive logistics, the multi-layered security of the intermodal system provides superior risk mitigation against both theft and transit damage.
Factor 5: Cross-Border Efficiency (USMCA)
The North American automotive supply chain is a testament to international integration, with parts flowing constantly between Mexico, the United States, and Canada. The efficiency of crossing these borders is a major factor in the overall performance of your logistics network.
- Trucking at the Border: Each truck is a discrete event at the border. It must queue and be processed individually. While programs like FAST/C-TPAT can expedite this, any truck can still be flagged for a secondary inspection, causing a delay for that specific load. Congestion at major crossings like Windsor-Detroit or Laredo can be unpredictable, and a customs issue or protest can create a significant bottleneck that halts the flow of parts for hours or days.
- Intermodal at the Border: A Streamlined System. The rail network was purpose-built for high-volume, cross-border commerce. A train carrying hundreds of containers crosses the border as a single, fluid unit. The customs process is highly streamlined and largely electronic:
- Pre-Clearance: Customs declarations are typically filed electronically while the train is still in transit.
- In-Bond Shipments: The most powerful tool is the ability to move a container “in-bond.” This allows the container to cross the physical border without being cleared and proceed directly to a bonded inland terminal (like those in the Greater Toronto Area). Final customs clearance is handled at this less congested inland location, completely bypassing the potential for delays at the busy land border.
This system is designed for the repetitive, high-volume shipments that define automotive logistics, offering a more predictable and fluid process for keeping your cross-continental assembly lines running.
Factor 6: Sustainability as a Supplier Scorecard Metric
This is no longer a “soft” benefit; it is a hard-line commercial factor in supplier selection. To be a successful Tier 1, 2, or 3 supplier in today’s automotive industry, you must be aligned with the aggressive sustainability goals of your OEM customers.
- The OEM Mandate: Major automakers like Ford, GM, and Toyota have made public commitments to achieving carbon neutrality. These are not just press releases; they are core business strategies that dictate operational decisions. To achieve these goals, they are scrutinizing every aspect of their value chain, including the carbon footprint of their inbound logistics.
- The Supplier Scorecard: When an OEM evaluates its suppliers, it uses a scorecard that rates them on key metrics like cost, quality, and on-time delivery. Increasingly, a fourth category is being weighted heavily: environmental performance. A supplier’s ability to demonstrate a low-carbon supply chain is becoming a critical competitive differentiator.
- The Intermodal Advantage: This is where intermodal shipping provides a clear and quantifiable advantage. Imagine you and a competitor are bidding for a new contract. You both have similar pricing and quality standards. However, you have structured your logistics using intermodal for the long-haul portion, allowing you to prove a 75% lower carbon footprint for transporting your parts compared to your competitor’s truck-only model. In the eyes of a sustainability-focused OEM, you are the superior partner. You are not just providing a part; you are actively helping them achieve one of their most important corporate objectives. This can be the single factor that wins you the contract.
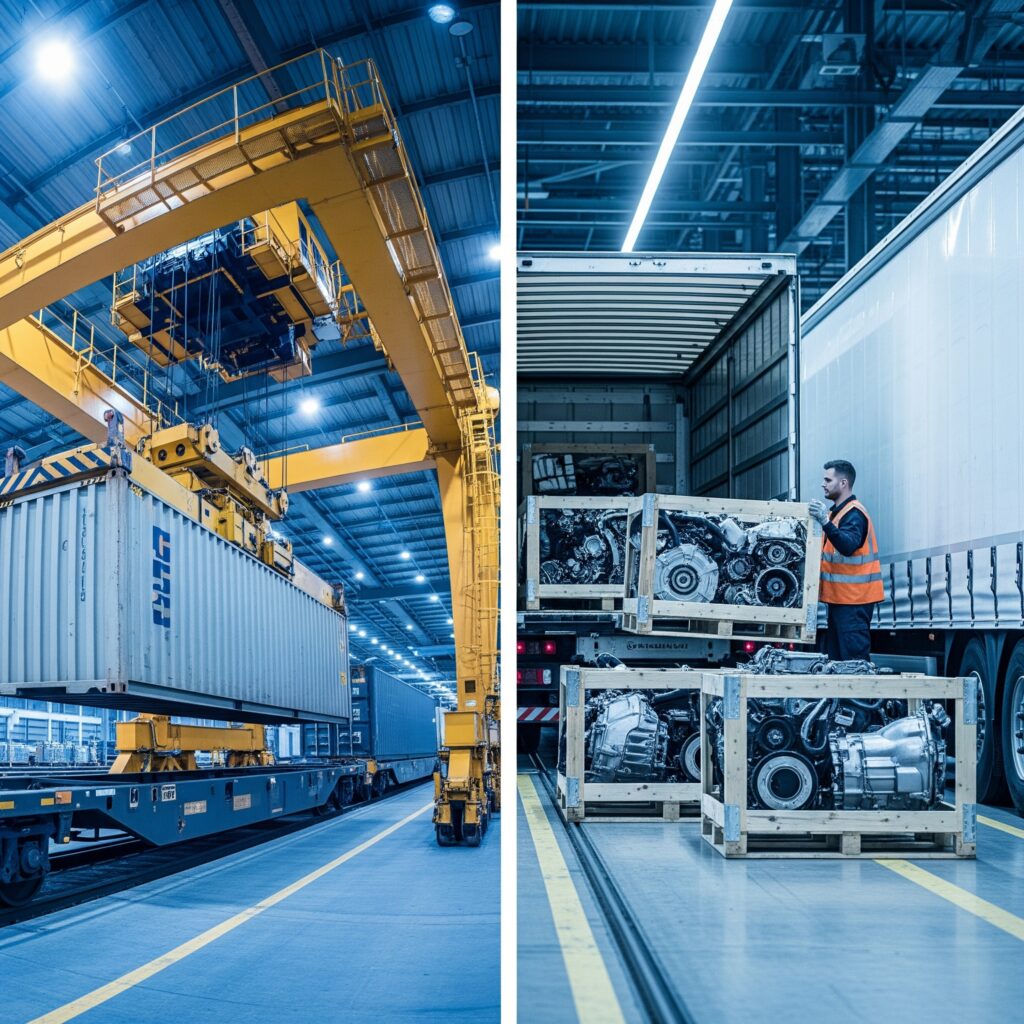
Part 3: The Decision Framework
After analyzing these critical factors, it becomes clear that the choice between intermodal and trucking is not a simple one. However, by synthesizing this information, we can build a sophisticated framework for making the optimal decision for your automotive supply chain.
Factor 7: The Hybrid Model – The Ultimate Automotive Logistics Strategy
The most common mistake in logistics planning is “all-or-nothing” thinking. The reality is that for a supply chain as complex and demanding as the automotive industry’s, the ultimate strategy is not to choose one mode over the other, but to intelligently integrate them into a sophisticated hybrid model.
Think of your logistics network as a diversified investment portfolio. A savvy investor doesn’t put all their capital into one high-risk stock or one low-yield bond. They build a balanced portfolio where different assets are used to achieve different goals—some for aggressive growth, others for stable returns and risk mitigation. A world-class automotive logistics strategy works exactly the same way. You leverage each transportation mode for its inherent strengths, creating a whole that is far more resilient, efficient, and cost-effective than the sum of its parts.
In this optimal hybrid model, each mode has a clearly defined and strategic role:
- Full Truckload (FTL) as the “Tactical Response” Fleet: Trucking remains an essential tool for its agility and go-anywhere flexibility. Its role in the hybrid model is tactical and specific. It is the perfect solution for:
- Short-Haul “Milk Runs”: For collecting parts from a cluster of local Tier 2 and Tier 3 suppliers located within a few hundred kilometers of your assembly plant.
- Emergency “Hot Shot” Shipments: When a critical parts shortage threatens a line-down situation, the raw speed of a dedicated truck is the necessary emergency response tool.
- Servicing Outliers: For delivering finished vehicles or aftermarket parts to dealerships and service centers in remote locations that are far from the main rail network.
- Intermodal Shipping as the “Strategic Backbone”:Intermodal shipping forms the core of the network, providing the foundation of reliability, cost-efficiency, and scale for all planned, high-volume movements. Its role is strategic and foundational. It is the ideal solution for:
- High-Volume Inbound Parts: For all your scheduled, long-haul shipments from distant Tier 1 and Tier 2 suppliers, especially those on the critical north-south USMCA trade corridor.
- Planned Inventory Replenishment: For moving aftermarket parts from central manufacturing plants to your network of regional distribution centers across North America.
- Outbound Finished Vehicles: For the mass distribution of new vehicles from your assembly plant to major metropolitan markets and port facilities for export.
By adopting this balanced approach, you stop trying to force one tool to do every job. You no longer overpay for trucking on long-haul lanes where intermodal is superior, and you don’t try to use intermodal for short-haul, urgent moves where trucking excels. This strategic allocation of resources is the hallmark of a truly optimized and modern automotive supply chain.
Conclusion: Making the Strategic Choice for Your Supply Chain
The choice between intermodal shipping and full truckload is not about declaring one mode universally “better” than the other. It is about making a sophisticated, data-driven decision to apply the right mode, to the right lane, for the right reason. For the high-stakes world of automotive logistics, where every minute and every dollar counts, this strategic approach is no longer just an option—it is essential for building a competitive advantage.
A supply chain that relies solely on trucking is vulnerable to price volatility, capacity shortages, and environmental pressure. A modern, resilient, and cost-effective supply chain must be multi-modal. By understanding the specific strengths of each mode—the tactical agility of trucking and the strategic power of intermodal—you can move beyond simple freight booking and begin architecting a logistics network that truly serves the demanding needs of your business.
The theory is clear. The next step is to see your own numbers.
Contact our automotive logistics team for a complimentary, no-obligation Lane Analysis. We will compare the all-in costs and transit performance of intermodal vs. trucking on your key routes, giving you the data you need to make a powerful business case.
Request Your Complimentary Lane Analysis Today
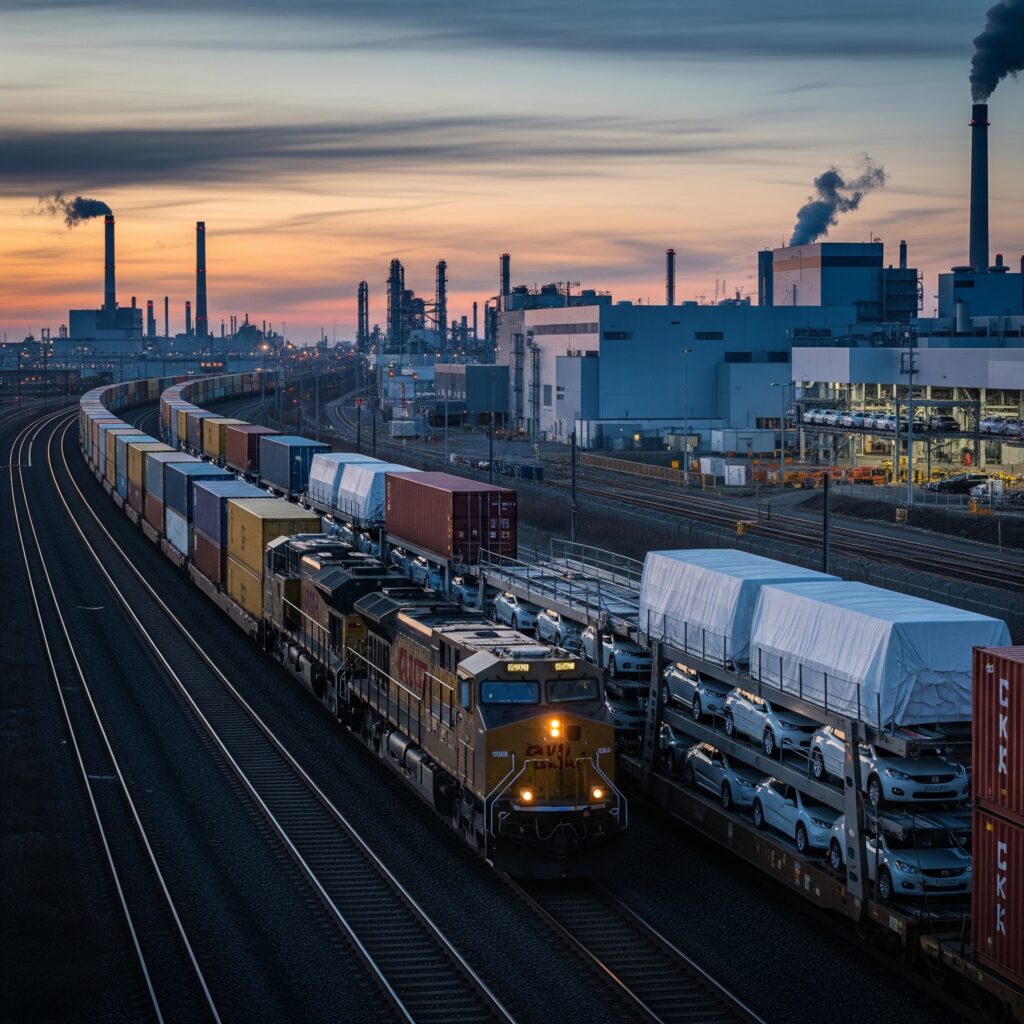
Additional Resources:
Intermodal Shipping with RailGateway
Automotive Intermodal Shipping
Canadian Vehicle Manufacturers’ Association (CVMA)
Automotive Parts Manufacturers’ Association (APMA Canada)
Automotive Logistics – Ultima Media
Government of Canada – The Canada-United States-Mexico Agreement (CUSMA)